Details
A tension control dancer is an essential component in a wire flattener machine, and it plays a crucial role in ensuring the quality and consistency of the flattened wire. Here’s why a tension control dancer is required:
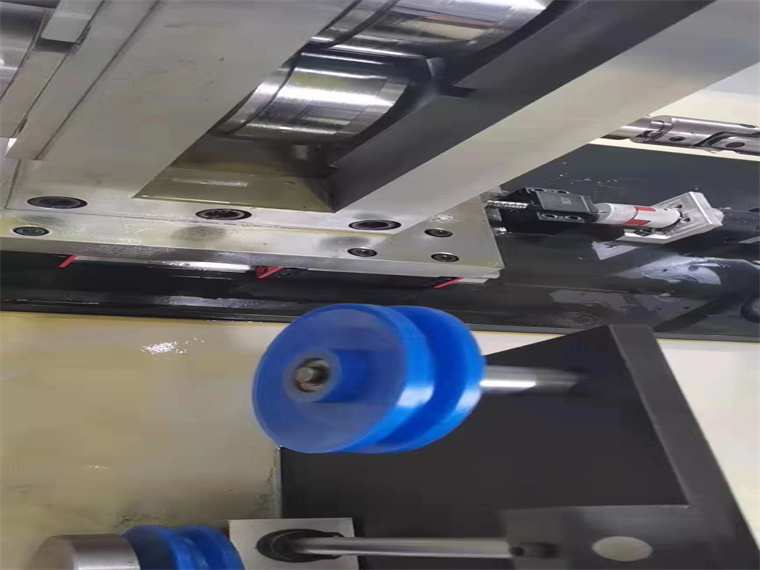
1. Maintaining Consistent Tension
Uniform Thickness: Consistent tension is vital for maintaining uniform thickness throughout the wire. Variations in tension can cause the wire to flatten unevenly, leading to thickness variations and defects.
Quality Control: Consistent tension helps in achieving high-quality surface finish and dimensional accuracy. Any fluctuations in tension can result in irregularities that compromise the quality of the final product.
2. Preventing Wire Breakage
Stress Management: Wire, especially thin or delicate wire, is susceptible to breaking under sudden changes in tension. The dancer system absorbs and compensates for these changes, preventing breakage and ensuring a continuous production process.
Smooth Operation: By maintaining a steady tension, the dancer system allows the machine to run smoothly without sudden jerks or stops, which could damage the wire or the machine itself.
3. Compensating for Speed Variations
Synchronization: In a wire flattening process, the speed at which the wire enters and exits different stages of the machine can vary. The dancer system helps synchronize these speeds by adjusting the tension dynamically.
Flexibility: The dancer allows the machine to handle variations in speed and tension that occur during normal operation, such as start-up, shutdown, or changes in processing speed.
4. Improving Productivity
Continuous Operation: With consistent tension control, the machine can operate continuously at higher speeds without frequent stoppages for adjustments or repairs due to tension-related issues.
Efficiency: By minimizing defects and breakage, the dancer system reduces waste and increases the overall efficiency and productivity of the wire flattening process.
5. Enhancing Process Control
Precision: The dancer system provides precise control over the tension, which is critical for producing high-precision flat wires, especially in applications where exact dimensions and high surface quality are required.
Automation: Modern wire flattening machines often incorporate automated control systems where the dancer is integrated into the feedback loop, allowing for real-time adjustments and improved process control.
6. Adaptability to Different Materials
Versatile Applications: Different materials have different mechanical properties and may require different tension settings. A dancer system allows the machine to be adaptable to a wide range of materials by providing the necessary tension control adjustments.
A tension control dancer is a vital component in a wire flattener machine because it ensures consistent tension, which is crucial for maintaining the quality, uniformity, and integrity of the flattened wire. It helps prevent wire breakage, compensates for speed variations, improves productivity, enhances process control, and allows for adaptability to different materials. These factors collectively contribute to the efficient and reliable operation of the wire flattening process.
The Following Are Some Of Our Classic Models From Our Wire Flattener Mill Machine with Tension Control Dancer Series:
How Else Can We Help You?
Flat Wire Rolling Mill
Wire Flattening And Shaping Lines
Machine For Flattening Copper Wire
Wire Shaping Lines For Carbon Steel Wires
Flat Wire Rolling Mill
Copper And Aluminum Flat Wire Drawing Machine
PV Ribbon Machine With Tin Coating Lines
Micro Rolling Cassettes
Titanium Alloy Wire Drawing Machine
Contact Us Today
Email:[email protected]
Mobile/Whatsapp:+86 13861313954
Website: https://precision-rolls.com/Products/