The process of producing carbon steel flat wire involves several stages that are critical to achieving the desired properties and dimensions. Below is a detailed description of each stage:
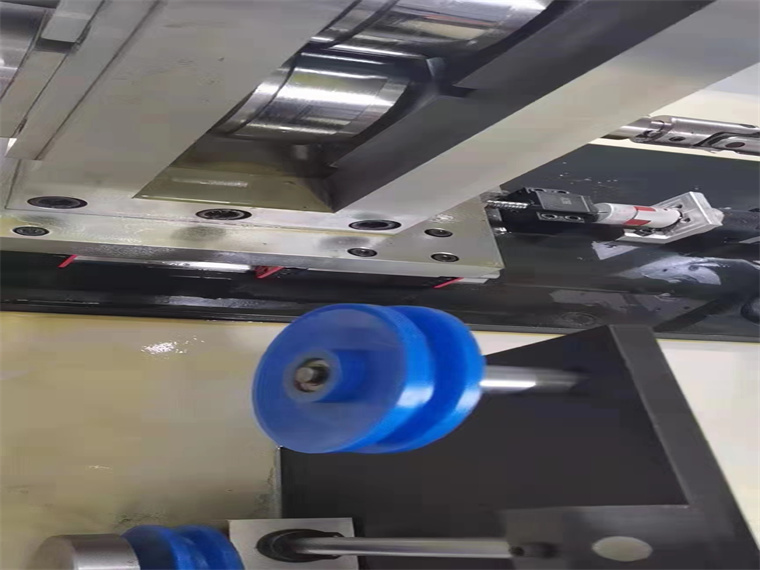
1. Raw Material Selection
First, we need to select the right grade of carbon steel round and flat wire. The steel composition, including the levels of carbon steel flat wire and other alloying elements, determines the final flat wire's mechanical properties.
2. Melting and Casting
Once the steel is melted, it is cast into billets or slabs through continuous casting, which serve as the starting materials for further processing. This can be accomplished by using an electric arc furnace or a basic oxygen furnace.
3. Hot Rolling
After billets or slabs are heated to a high temperature, they are rolled carbon steel flat wire through a series of rolling mills to reduce their thickness. For carbon steel flat wire, this strip will later be further processed to achieve the desired dimensions.
4. Pickling
In order to remove scale and oxides formed during hot rolling, hot-rolled steel strips are picked, which involves immersing them in an acid bath, usually hydrochloric or sulfuric acid, and rinsing and drying them.
5. Cold Rolling
After cleaning, the strip is cold-rolled to further reduce its thickness and improve surface finish. Cold rolling works by passing the strip between rolling stands at room temperature, thereby work hardening the steel and enhancing its mechanical properties.
6. Annealing
In order to reduce the internal stresses introduced during cold rolling for low carbon steel flat wire and to adjust the mechanical properties, the cold-rolled strip is annealed. Annealing involves heating the strip to a specific temperature and cooling it at a controlled rate.
7. Flattening
As soon as the strip is annealed, it is flattened to ensure there are no curvatures or wavinesses. This can be achieved through the use of cold rolling high carbon steel flat wires or specialized carbon steel wire flattening equipment.
8. Slitting
Slitting involves cutting the flat strip longitudinally to create narrower strips, which are further processed into flat wire.
9. Edge Conditioning
In order to achieve the desired edge profile, the edges of slit strips are deburred, edge rolled, or edge shaved to remove any burrs.
10. Final Cold Rolling (Flattening)
To achieve carbon steel flat wire thicknesses and flatnesses, the slit strips are passed through cold rolling mills or flattening mills.
11. Surface Treatment
In order to improve corrosion resistance or other surface properties, flat wires may undergo surface treatments such as coatings, platings, or passivations.
12. Quality Control and Inspection
Quality control measures are applied throughout the process to ensure the carbon steel flat wire meets the required specifications, including dimensional checks, mechanical property tests, and surface quality tests.
13. Packaging and Shipping
After the carbon steel flat wire has been finished, it is coiled or spooled, packaged, and shipped, depending on the length required.
Multi-stage processes ensure the carbon steel flat wire has the mechanical properties, dimensions, and surface quality required for its intended use.
Are You Looking for a Carbon Steel Flat Wire Machine?
Here are the models I recommend for you
Wire Flattening And Shaping Lines Machine For Flattening Copper Wire Wire Shaping Lines For Carbon Steel Wires Flat Wire Rolling Mill Copper And Aluminum Flat Wire Drawing Machine PV Ribbon Machine With Tin Coating Lines Micro Rolling Cassettes Titanium Alloy Wire Drawing Machine Profile Wire Rolling Lines For Piston Rings Copper Strip Rolling Mill Ultra Precision Rolling Mills Flat Magnet Wire Equipment Straight wire drawing machine Copper And Aluminum Flat Wire Drawing Machine