Industry Standards for Titanium Alloy Wire Production Equipment
In aerospace, medical, automotive, and more, titanium alloy wires are indispensable components. Manufacturers are investing in advanced production equipment to meet the rising demand for high-quality titanium alloy wires. This article examines the importance of titanium alloy wire production equipment and how it ensures compliance with industry standards.
Machinery that is precision-made
Advanced CNC (Computer Numerical Control) machines play a crucial role in shaping and forming titanium alloy wires with precision and consistency. Precision machinery is one of the fundamental elements of titanium alloy wire production. These machines are programmed to follow precise specifications, ensuring the wire's diameter, surface finish, and mechanical properties meet the required standards.
The melting and alloying of metals
In order to create the desired titanium alloy composition, titanium and other selected metals are melted and alloyed together. An induction melting furnace provides excellent temperature control and produces high-quality alloys at this stage. For the wire product to possess the desired properties, it is crucial to maintain the right alloy composition.
The Drawing and rolling process
An alloy is prepared and then extruded using specialized equipment. In Wire drawing process, molten alloy is forced through a micro rolling casstte die in order to form a wire. It is possible to control the wire's diameter precisely and customize its size and shape using this rolling and cold drawn process.
The drawing and annealing process
Following drawing, the wire is pulled through a series of roller dies to reduce its diameter further. In addition to improving the wire's mechanical properties and surface finish, annealing is performed to relieve any stresses and enhance its ductility after drawing.
Controls and tests for quality
Throughout the production process, quality control measures are implemented to ensure the titanium alloy wire meets industry standards. To detect faults or defects in wires, non-destructive testing techniques such as ultrasonic testing and eddy current testing are commonly used. In addition, mechanical testing is performed to verify wire strength and flexibility.
Inspection and packaging of the final product
The wire undergoes a final inspection once it meets all quality criteria before being packaged for shipment. The packaging ensures that customers receive complete traceability and compliance data with the product. Proper labeling and documentation prevent damage during transportation and storage.
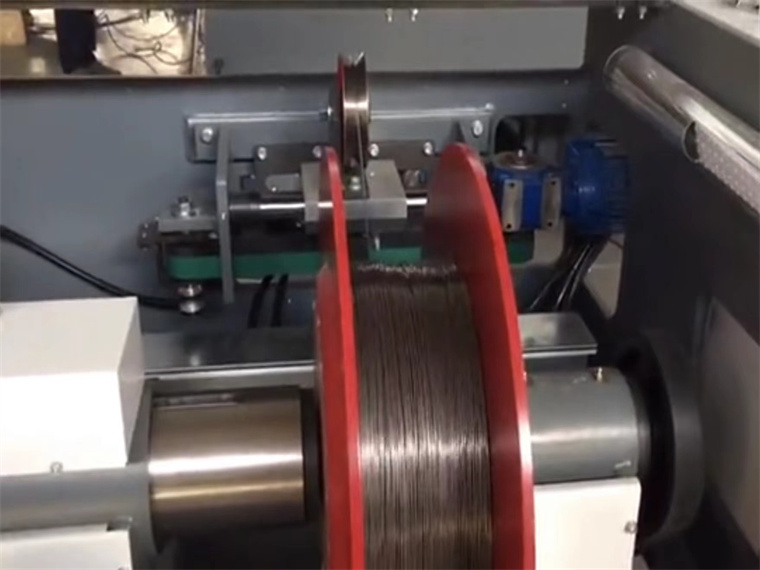
As a conclusion
Precision, consistency, and adherence to strict industry standards are required to produce titanium alloy wires. In order to achieve these objectives, advanced production equipment, including CNC machines, induction melting furnaces, and extrusion systems, are crucial. It is very important for manufacturers to ensure that their equipment and processes produce titanium alloy wires that meet the stringent requirements of aerospace and medical industries. Due to the growing demand for these high-performance wires, reliable production equipment is essential.
The following are some of our common models for Titanium Alloy Wire Production Equipment
Titanium-Alloy-Wire-Machine
Nickel-Silver-Wire-Drawing-Machine
Nickel-Wire-Drawing-Machine
Titanium-Alloy-Wire-Drawing-Machine
Contact us for more information
[email protected]
whatsapp:+86 13861313954
https://precision-rolls.com/Products/