Advancements in Wire Drawing Technology: The Rise of Cold Rolling Cassette Mode Wire Drawing Machines
In traditional wire drawing machine production, the process relies solely on wire drawing dies to complete the operation. This involves drawing the wire through a series of wire drawing dies to reduce its diameter, thereby enhancing its mechanical properties and surface quality. However, with the evolving demands of users for diverse finished products, cold rolling cassette have increasingly replaced conventional wire drawing dies in certain applications. Machines utilizing this advanced approach are referred to as cold rolling cassette mode wire drawing machines, a specialized category of dry wire drawing machines. This innovation represents a significant step forward in meeting industry-specific requirements with improved efficiency and versatility.
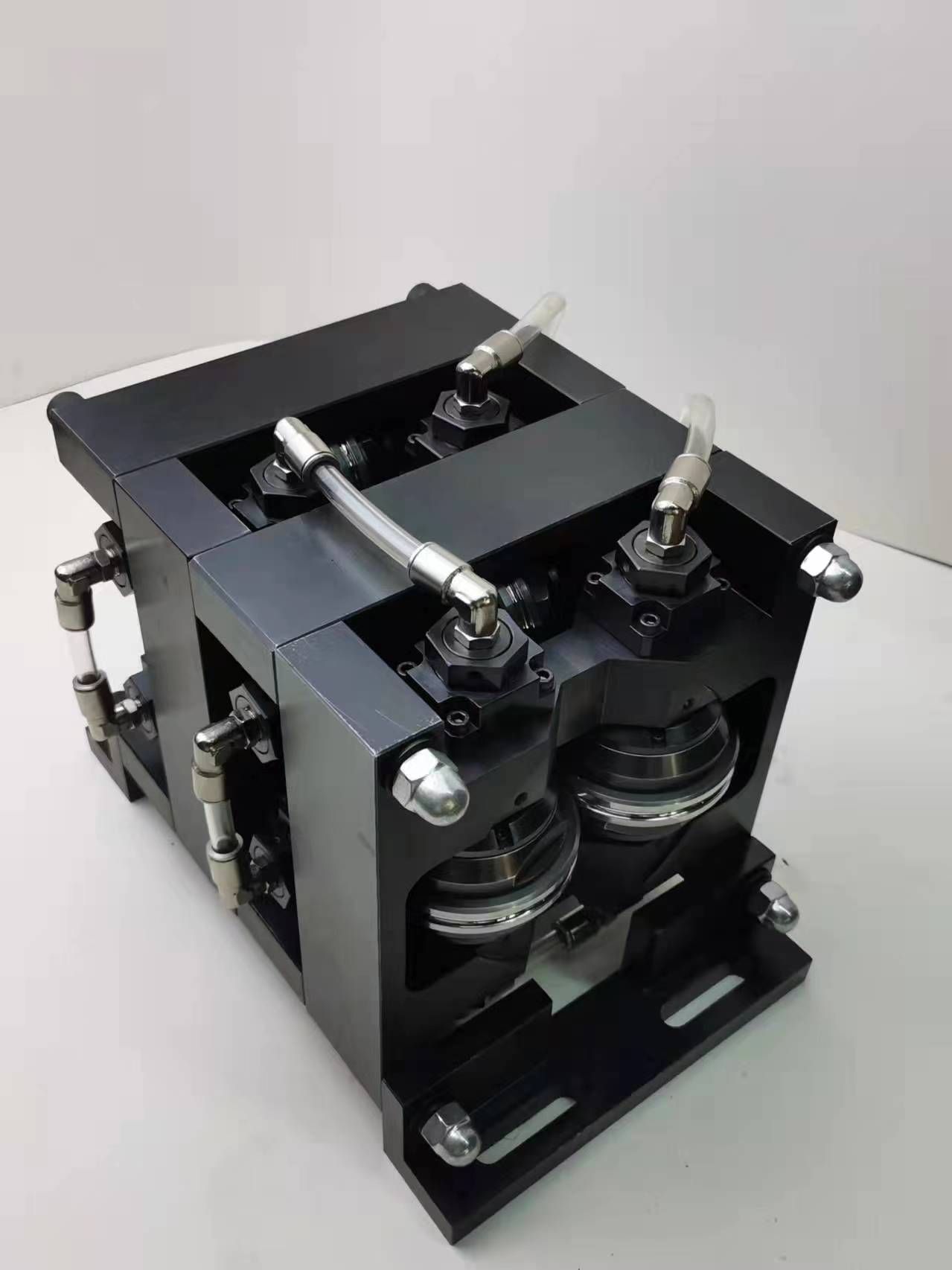
Direct Drive Servo Motor Dry Micro Wire Drawing Machine for Carbon Steel Wires
The Direct Drive Servo Motor Dry Micro Wire Drawing Machine for Carbon Steel Wires is an innovative solution designed for high-precision wire drawing applications. As a representative model in the rolling cassette-type wire drawing machine series, it integrates cutting-edge direct drive servo motor technology, offering exceptional precision and efficiency for processing carbon steel wires.
This direct wire drawing machine features a dry drawing mechanism, significantly reducing lubrication requirements, lowering operating costs, and minimizing environmental impact while enhancing wire surface quality. Its versatility shines in flexible production scenarios: if users need to quickly process a new specification or small batch without the appropriate roller specifications, the cassette roller die can be easily swapped for a wire drawing die box to accommodate various production needs.For users with multiple wire drawing machines, the roller die wire drawing machine can primarily produce fixed-specification products, with effortless roller replacements enabling smooth transitions to different specifications when required.
Cold Rolling Cassette: Boost Productivity and Precision with Advanced Wire Drawing Technology
The cold rolling cassette is a versatile innovation designed to be installed on your existing wire drawing machines, replacing traditional wire drawing dies. It consists of a set of rollers made from highly wear-resistant materials, such as tool steel or carbide steel, finely processed to achieve precise hole configurations. The number of rollers, typically ranging from 4 to 10, is customized based on the material, wire diameter, and required surface reduction rate.
During operation, the wire passes through the roller die, where the rollers rotate due to the tension and friction between the wire and the roller holes. This process reduces the wire’s diameter with exceptional precision. Standard roller dies produce wires with a diameter tolerance of ±0.02mm, while special roller models achieve a tolerance of ±0.01mm.
The longevity of rollers depends on factors such as the processed material, surface conditions, and maintenance management. In practice, wear is often measured by the processed material's weight rather than length, reflecting production habits. Additionally, worn rollers can be refurbished and adapted for other specifications, much like repairing wire drawing dies, offering a cost-effective and sustainable solution for manufacturers.
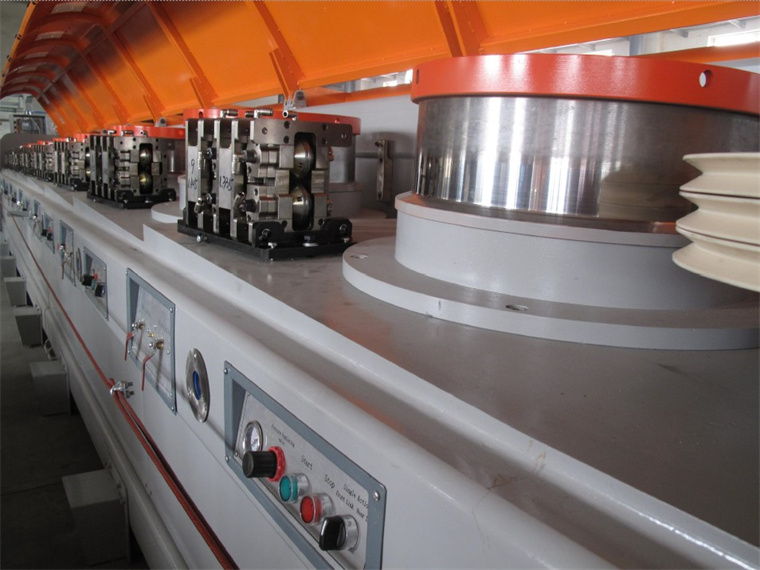
How Rolling Cassettes Integrate into Wire Drawing Machines
Rolling cassettes are an innovative upgrade for traditional wire drawing machines, designed to enhance precision, efficiency, and flexibility. These components replace conventional wire drawing dies and are installed seamlessly onto existing machines with minimal adjustments. Comprising high-strength rollers made from tool steel or carbide, rolling cassettes are tailored to match wire material, diameter, and reduction needs, with configurations ranging from 4 to 10 rollers.
During operation, wires pass through precision-engineered roller holes, where tension and friction drive roller rotation. This process ensures consistent diameter reduction while maintaining superior surface quality. Rolling cassettes also offer remarkable versatility, allowing manufacturers to switch between roller setups or revert to standard die boxes to meet varied production demands.
With regular maintenance and the ability to refurbish worn rollers, rolling cassettes provide a cost-effective and sustainable solution for modern wire drawing operations, boosting productivity and achieving tighter tolerances for high-quality outputs.
Which Materials Are Suitable for Rolling Cassette-Type Wire Drawing Machines?
Rolling cassette-type wire drawing machines are designed to process a broad range of materials, meeting the diverse requirements of various industries. These machines excel in handling carbon steel, stainless steel, solid welding wire, flux-cored welding wire, alloy steels, and titanium wire. They are also highly effective for non-ferrous materials such as copper, aluminum, and brass, which are extensively used in sectors like electronics and automotive manufacturing. With their versatility and precision, rolling cassette-type wire drawing machines deliver exceptional performance across a wide spectrum of applications.The multi-channel wire drawing machine replaces the single-channel wire drawing machine, which is a technical upgrade and transformation of the steel wire drawing machine. The continuous drawing adopted by the wire drawing machine greatly improves the production efficiency;
Contact Us Today
Email:[email protected]
Mobile/Whatsapp:+86 138 6131 3954
Website: https://precision-rolls.com/Products